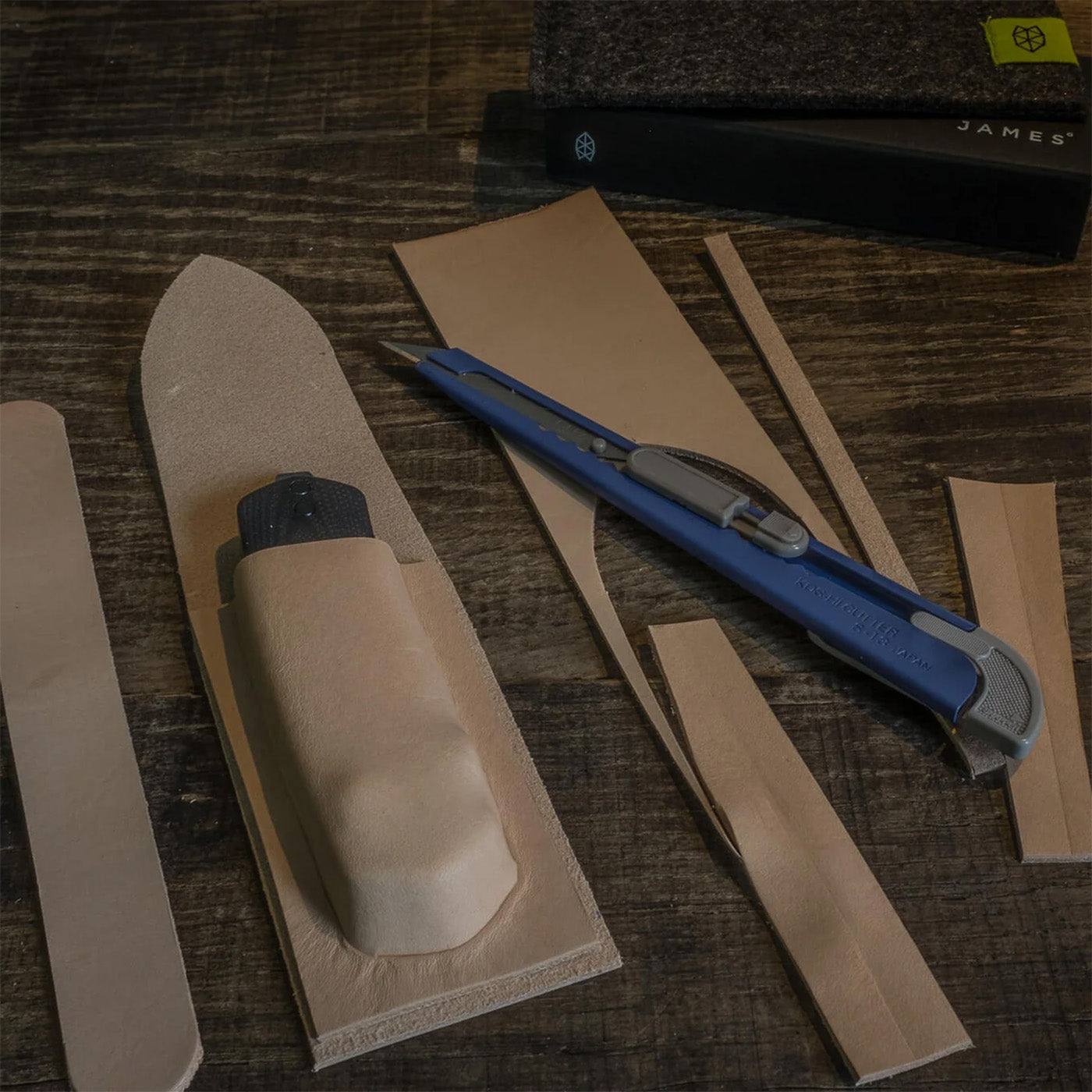
How to make a leather knife sheath for a 'James Knife'
One of the benefits of being a craftsman, is making custom orders. The cherry on the cake is when we receive a product as the James knife.
As they say at The James Brand:
We make products for your everyday.
We make knives and tools for people who live adventurously - for people like us. For those who aren’t content consuming other people’s stories, and who don’t wait around for other people to fix things. We're with you, from the pocket to the hand, and back again.
So definately this will fit Duke & Sons.
Here is the visual story of 'the making of the James Knife leather sheath'


First we use a piece of Forex and draw the outline of the knife.

Using a jigsaw to make a mold.


Cutting a piece of vegetan leather.

Soaking the vegetan leather.

Wrapping the James Knife in foil.
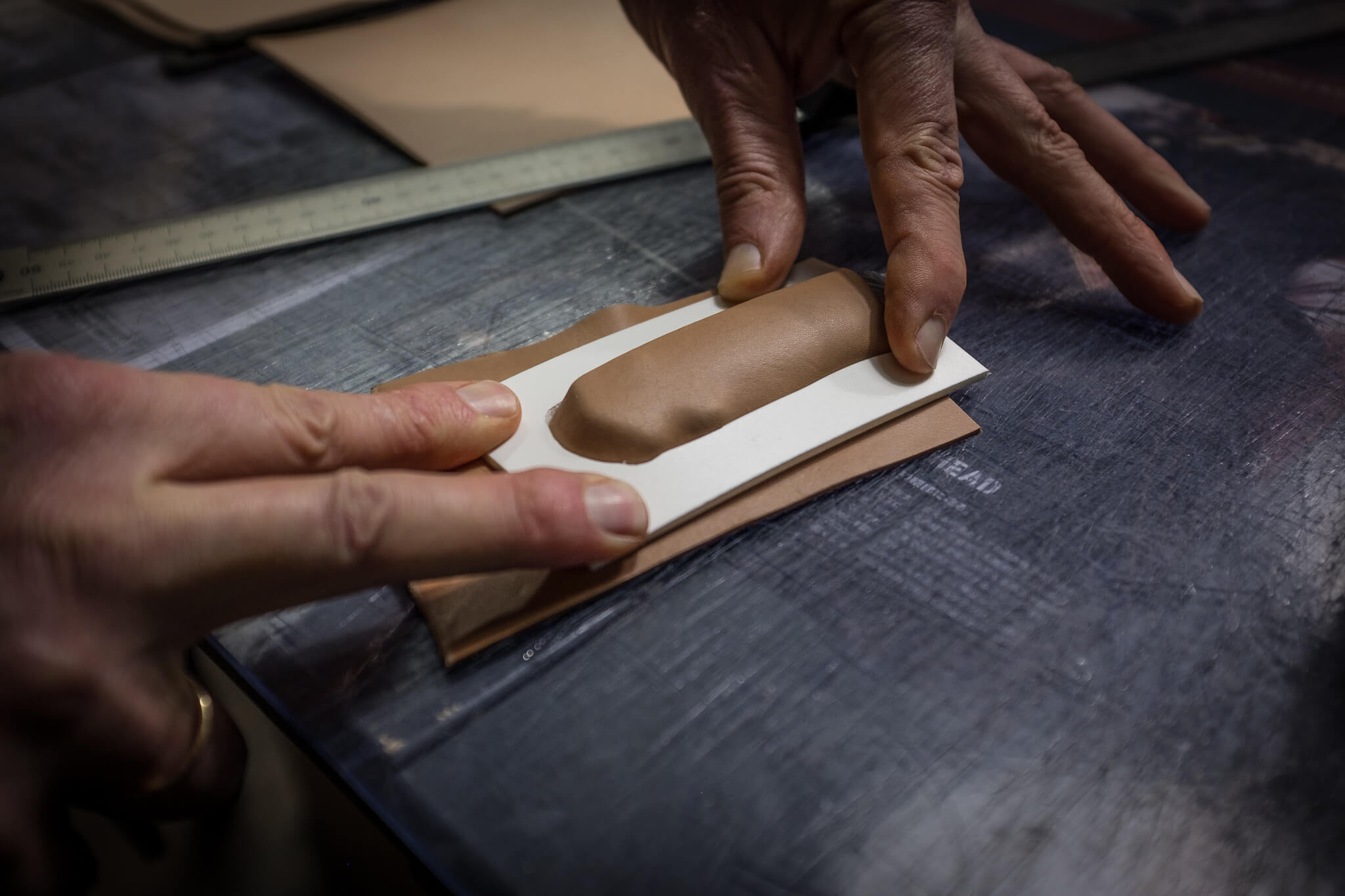
Positioning the soaked leather and the mold.

Clipping the mold and let it dry overnight.

Dry, and in the perfect shape.

Cutting the remaining parts.

The dying process take several stages to get the expected color.

Dying is done and now we let it dry overnight.

Finishing the leather with a thin, acrylic, top finish that will give it a medium shine and provide some water resistance.

Buffing with a good brush for some extra shine.

Adding the belt loop.

Adding leather glue to both parts, let it dry for a while and stick together.

When parts are fixed we sand the edges.

Beveling the edges.

Marking the stitch holes line.

Punching the stitching holes using the Crimsonhides pricking iron 4mm (see my blogpost: https://www.dukeandsonsleather.com/blogs/maker-stories/handstitching-pricking-iron-chisel-looking-for-the-perfect-stitch)

Ready for the next stept: sanding, dying and burnishing the edges.

Burnishing the edges together as one.
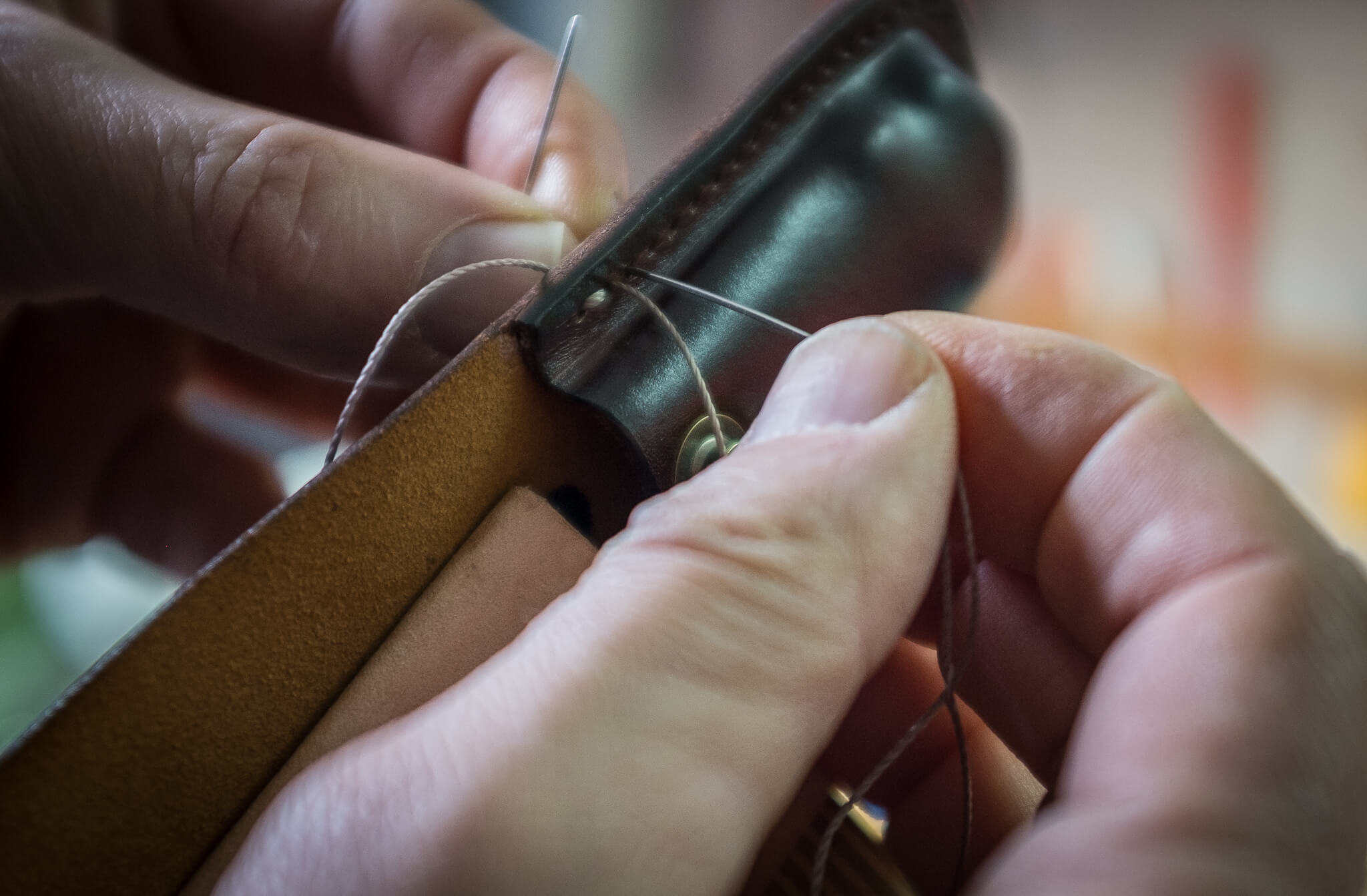
Handstitching with Crimsonhides Japanese Polyester thread.
(https://crimsonhides.com/collections/leathercrafting-supplies/products/mbt-polyester-threads-0-5mm-70m)

Adding an extra rivet at the top corners.

Done! The handmade leather James Knife sheath!